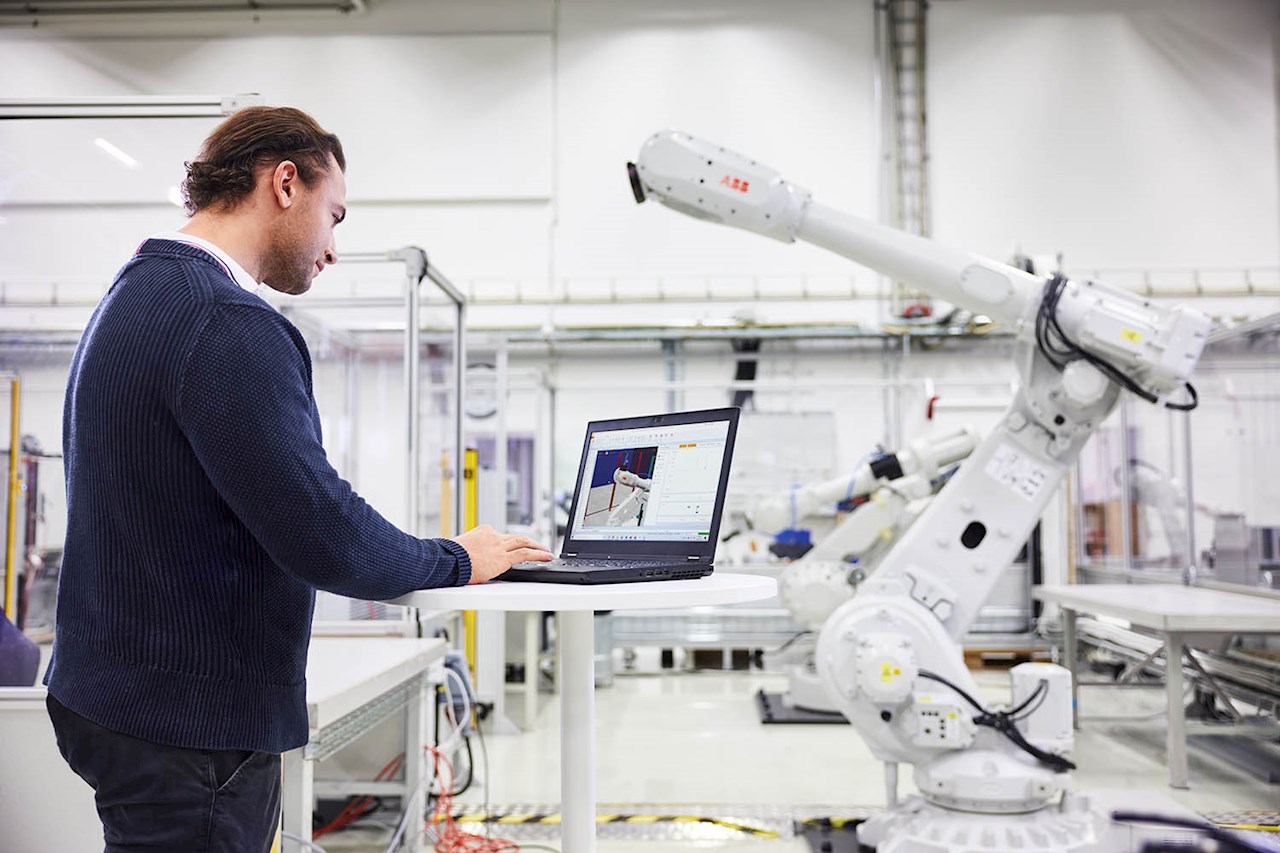
offline programminig
What is offline programming and why is it so crucial today?
Here, we’ll delve into robotized industrial processes that we meticulously realize through advanced programming and on-field experience.
Offline programming, within the realm of industrial robotics, represents an advanced approach enabling the design, creation, and optimization of robot programs outside the production environment, thus making the implementation of most industrial processes possible.
Here are the reasons why it’s crucial today.
Reducing Robot Downtime
It allows for the development and optimization of robot programs without interrupting ongoing production, reducing downtime and increasing overall productivity.
Path and Cycle Time Optimization
Virtual commissioning
“Virtual commissioning” involves using simulation software and virtual models to test and validate the operation of a complex system before it is physically built or implemented.
In the context of industrial plant control and automation, the “commissioning” phase is the final process in which the system is installed, tested, and started up to ensure that it functions properly according to the required specifications. The “virtual
commissioning” allows performing these activities in a virtual environment before physical construction takes place, offering various benefits:
- Cost Reduction. Early error resolution through simulations can reduce costs associated with modifications and repairs after physical construction.
- Time Savings. Virtual commissioning reduces the overall time required for the commissioning process, as many activities can be performed simultaneously.
- Design Optimization. Simulations allow for optimizing the system design before physical construction, helping to identify and address potential issues more efficiently.
- Staff Training. Personnel involved in operation and maintenance can be trained using virtual simulations, better preparing them to handle real system challenges.
Digital twin
The concept of a “Digital Twin” refers to creating a digital replica of a physical object, process, or system from the real world. This digital replica is a virtual representation that reflects in real-time the state and behavior of the corresponding object or system.
Implementing digital twins can lead to more efficient, predictive, and personalized management of resources and processes. Technology is constantly evolving, and digital twins are becoming increasingly central in the era of Industry 4.0 and advanced connectivity.
Collision Risk Reduction
Agility and Adaptability
Simplification of Staff Training
Optimal Resource
Increased Production Flexibility
Ease of Maintenance and Diagnosis
In summary, offline robot programming offers a strategic approach to improving production management, optimizing robot usage, and reducing downtime associated with traditional on-site programming.
Offline programming processes
In our experience, we have had the opportunity to delve into various offline programming processes. Here are the processes we have worked on.
PROCESSING
Deburring
During various casting operations performed by special machines, burrs, chips, or excess materials can form at the edges of components. These burrs are small residues that can, on one hand, create problems for the mechanical function of the final product, and on the other hand, also increase the risk of injuries.
For this reason, when producing complex metal parts for hot stamping, it is necessary to remove this excess material during the finishing process.
Robotic deburring can be performed on a variety of materials used in different industrial sectors. Below is a list of some common materials on which we perform robotic deburring processes.
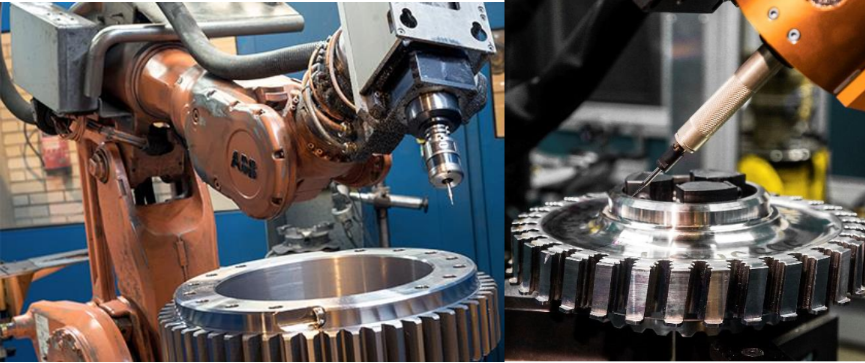
Metals
- Stainless steel
- Aluminum
- Carbon steel
- Brass
- Titanium
- Metal alloys
Special Alloys
- Aerospace aluminum alloys
- Titanium alloys for medical applications
- Special alloys for specific sectors (e.g., automotive, aerospace)
It is important to note that robotic deburring may require specific solutions based on the characteristics of the material, surface geometry, and the type of deburring required. The choice of the appropriate process and tools will depend on the specific requirements of the application and material.
PROCESSING
Adhesive Bonding
Industrial bonding is a manufacturing procedure that involves applying adhesives or glues to specific materials in order to permanently bond them.
This process is essential for creating strong and reliable adhesive joints, offering an effective and versatile alternative to traditional fastening techniques such as welding or screws.
In robotic bonding, various types of adhesives are used based on the specific requirements of the application and materials involved. Below are some of the main types of adhesives we have used in this context.

Epoxy
Adhesives based on epoxy resins known for their strength, durability, and ability to adhere to a wide range of materials, including metals, plastics, and composites.
Acrylics
Adhesives based on acrylic resins that offer good resistance to mechanical stress and temperature variations. They are suitable for assemblies of different materials.
Cyanoacrylates (Cyano)
Fast-setting cyanoacrylate-based adhesives that polymerize quickly in the presence of moisture, ideal for quickly bonding materials such as plastic, rubber, and metals.
Polyurethanes
Adhesives based on polyurethane resins with flexibility properties, suitable for joints subject to movements and flexions. They can be used on various materials.
Silicones
Adhesives based on silicone that offer high resistance to high temperatures and good adhesion to porous substrates such as glass and ceramics.
Hot Melt
Thermoplastic adhesives that become liquid at high temperatures and solidify rapidly when cooled, often used to bond materials such as cardboard, fabrics, and plastic.
Anaerobic
Adhesives that polymerize in the absence of oxygen and commonly used for threaded or screwed joints in industrial applications.
Thermosetting
Adhesives that harden through a thermal process, providing a stable and resistant connection.
UV Reactive Adhesives
Adhesives that polymerize through exposure to ultraviolet (UV) rays, providing rapid solidification and are often used for heat-sensitive assemblies.
The choice of adhesive type depends on various factors, including the materials to be bonded, joint properties required, environmental conditions, and application specifics. Compatibility with robotic bonding process, curing speed, and durability are crucial considerations in selecting the type of glue.
PROCESSING
Welding
Welding is a process of joining two or more parts by the action of heat, pressure, or both, sometimes achieving material continuity.
Welding can be classified into two families.
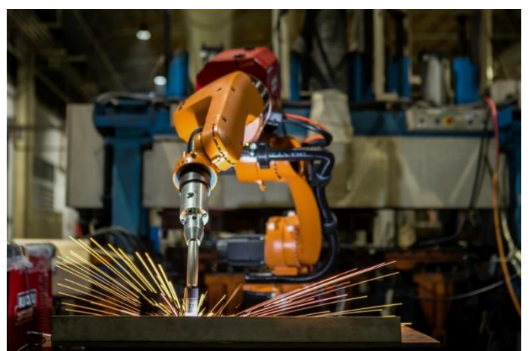
Autogenous Welds
The connection occurs through localized melting of the edges to be joined, with the possible addition of filler material; this way, structural continuity between the pieces is achieved.
Heterogeneous Welds
These are typical processes in brazing and soldering, in this case, the connection occurs through the fusion of only the filler material that lies between the edges to be joined, which do not even partially melt; structural continuity between the pieces is not achieved.
As we well know, welding methods can be varied; in the case of robotic welding, a welding head is commonly used, which can be arc (MIG or MAG), resistance (typically spot), TIG, or laser.
The main fields of application include industrial automation, aerospace and defense, transportation, energy and oil sectors, general manufacturing, construction, electronics industry, automation and robotics, machinery manufacturing, and food and beverage industry.
PROCESSING
Sandblasting
Sandblasting is a process whereby the outermost part of a material is eroded by abrasion from a jet of sand and air. The most common use is for the superficial cleaning of metals, but it can be used on many other surfaces.
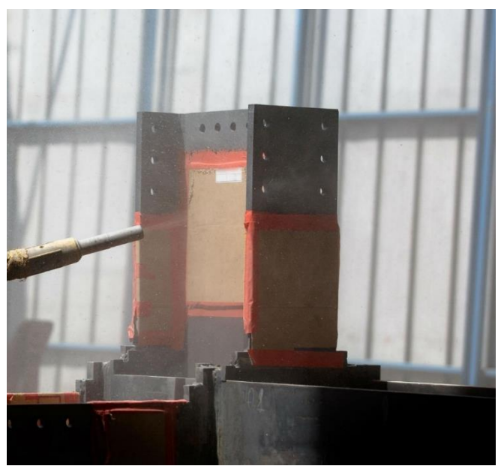
Sandblasting can be an intermediate or final procedure in the processing cycle of a product:
- intermediate sandblasting is used when the product will undergo further treatment;
- final sandblasting is used to give an aesthetic effect as a last treatment.
At the end of the process, the underlying material beneath the removed layer presents variable roughness depending on the size of the abrasive used and the jet pressure. Sandblasting is the best procedure for preparing the piece for subsequent painting. The most common materials on which it is performed are steel, cast iron, metal alloys in general, wood, and glass. The need to sandblast some materials arises from various needs:
- remove existing surface treatments such as oxides or paints;
- increase adhesion between materials;
- improve aesthetic appearance.
PROCESSING
Plasma Cutting
Plasma cutting is a thermal cutting process that uses a stream of ionized gas, known as plasma, to melt and remove metal material from a sheet or other form of metal. The plasma is generated by passing gas through a nozzle and applying an electric arc between the nozzle and the workpiece. This process creates a high temperature in the plasma, sufficient to melt and cut the metal and other materials.
This versatile technology finds application in various manufacturing sectors such as automotive, aerospace industry, shipbuilding, industrial machinery production, and many others…
In conclusion, plasma cutting offers significant advantages, including versatility in processing various materials, operating speed, and precision, making it an essential technology in multiple industrial contexts.
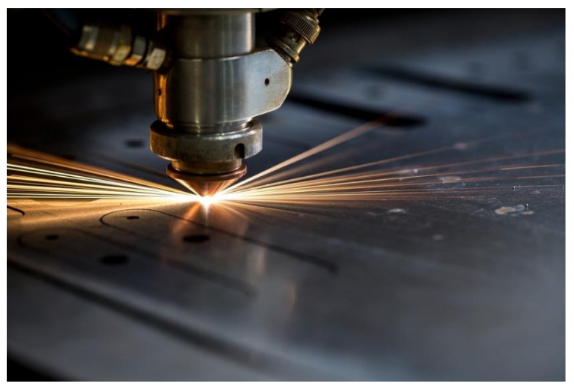
PROCESSING
Handling
Industrial robot handling involves the ability of robots to move, lift, and position objects precisely in industrial activities while respecting a specific cycle time.
Through offline programming, robots are able to perform handling tasks in dynamic, safe environments, focusing on cell feasibility and cycle time assessments.
This capability is crucial in sectors such as logistics, assembly, and material handling, contributing to improving productivity and achieving precise evaluations.
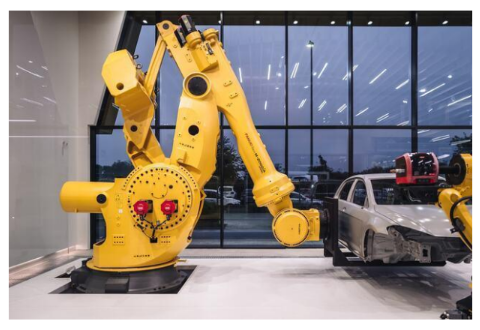
PROCESSING
Laser Hardening
Laser hardening is an advanced thermal process that involves using laser to rapidly heat a specific area of a material, followed by equally rapid cooling.
This process is often used to modify the surface properties of a material, such as hardness and wear resistance, without significantly altering its volumetric characteristics.
Laser hardening finds applications in sectors such as mechanical engineering, aerospace industry, tool manufacturing, electronic component fabrication, and other contexts where improving surface properties of materials without compromising their internal structure is crucial.

PROCESSING
Laser Welding
Laser welding is a materials joining process that utilizes the energy of a laser beam to melt the surfaces of the parts to be joined. This method offers numerous advantages, including precision, speed, and accurate thermal control. During laser welding, a high-intensity laser beam is focused on the joint area, generating enough heat to melt the material. This process is widely used in various industrial sectors, including the automotive and aerospace industries, for the production of high-precision components.
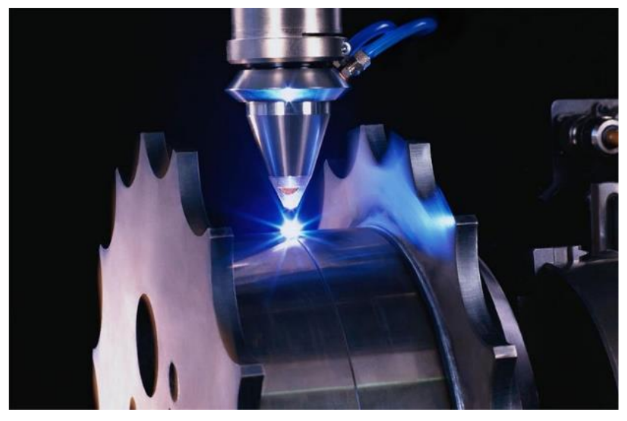
PROCESSING
Laser Cladding
Laser cladding is an advanced additive manufacturing and surface coating technique that uses a laser beam to deposit controlled layers of metallic material onto a substrate. This process is used to repair or enhance the characteristics of metal components, providing a precise and localized solution. During the operation, a powder or wire material is melted by the laser beam focused on the working surface, creating a solid and adherent coating. Laser cladding finds applications in sectors such as aerospace, automotive, and manufacturing, offering benefits such as wear resistance, corrosion resistance, and customized material properties. The technology is particularly useful for extending the service life of components and for the additive production of complex and high-precision parts.
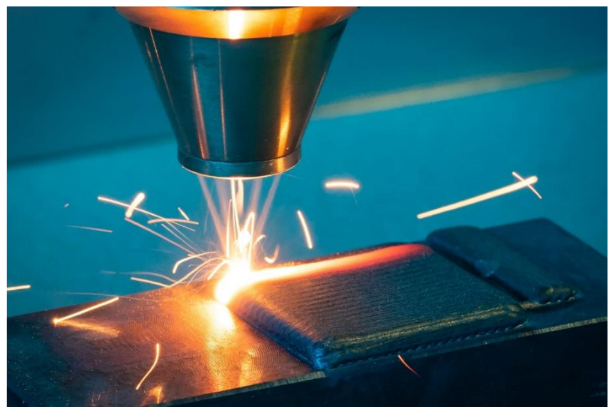
PROCESSING
Inspection and Quality Control
Developing inspection and quality control programs for components with cavities or hard-to-reach areas is as important as other processes. By using probes or micro-cameras, very tight spaces can be reached, and quality control of certain processes can be carried out.
In this case, the robot equipped with a probe or a tool with artificial vision is programmed to inspect the interior or surface areas of a component following a process.
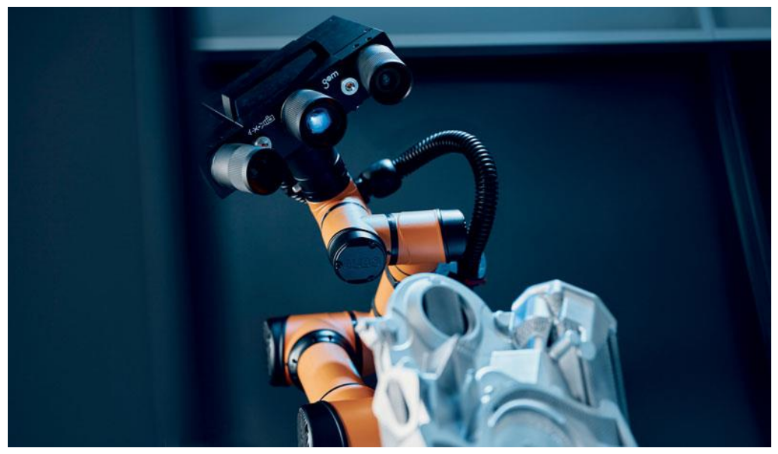
If you are interested in learning more about the various machining and offline programming solutions we have developed please contact us here.
CONTACT US
WRITE US TO HAVE A PERSONALIZED CONSULTATION
Via della Scienza, 50, 41122 Modena – Italy
+39 327 1945044
info@ideativa.it
